Achieving cost savings through value engineering which reduced pile lengths, managed geological variability and optimised load carrying capacity
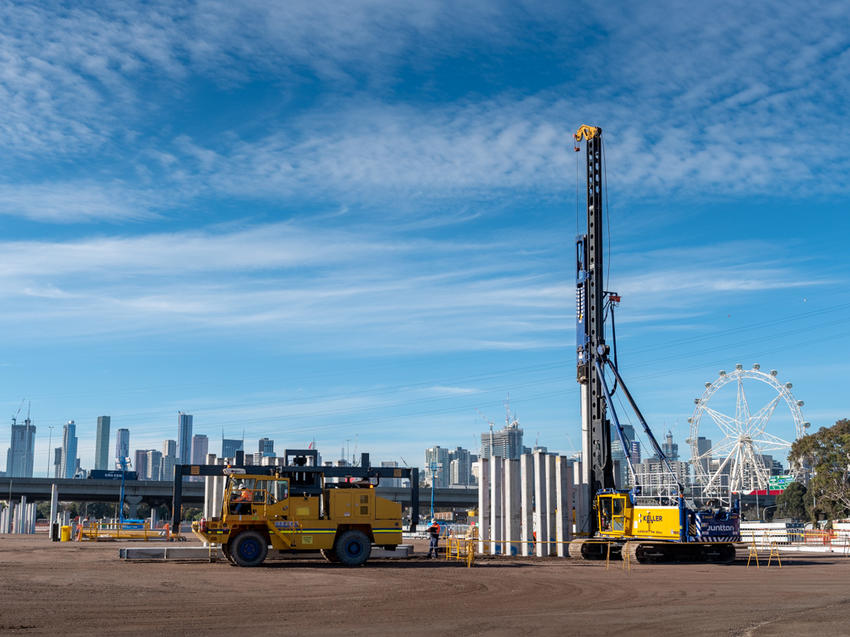
The project
The West Gate Tunnel Project will provide more than 15km of new elevated traffic lanes as a new major transport route to Melbourne’s Port. Part of Keller’s brief was to help challenge the existing state of practice in the market, with a critical focus on safety and product quality.
The challenge
Keller’s propensity for innovation and flexibility came to the fore in this project, with an opportunity to develop new piling-related processes that raise the bar in terms of industry safety. Conventional ways of practice needed to be constantly rethought. Structural issues also posed problems, with work carried out on an existing major arterial, and lower than usual headroom adding to the difficulty of driving piles.
The solution
One of the biggest safety issues involved the removal of above ground pile waste, a procedure that has traditionally involved a great deal of direct human interaction. Keller drew on its global expertise, sourcing ideas advice and ideas from a Polish Keller team who had used a technique while working on a gas field project in Kazakhstan. The result was a two-machine operation with no direct personnel interaction in the key exclusion zone. The original design for the precast piles suggested an average length of forty metres. However, on engagement with the project, Keller’s engineers felt that the same technical outcomes could be achieved with piles that were 25% shorter. On approval, Keller developed a program and a contract model that facilitated this change and provided the client with cost savings with no compromise on quality. Dealing with restricted headroom necessitated significant modifications to machinery not designed for this task but which were able to efficiently install the precast pile segments within the low headroom restrictions.
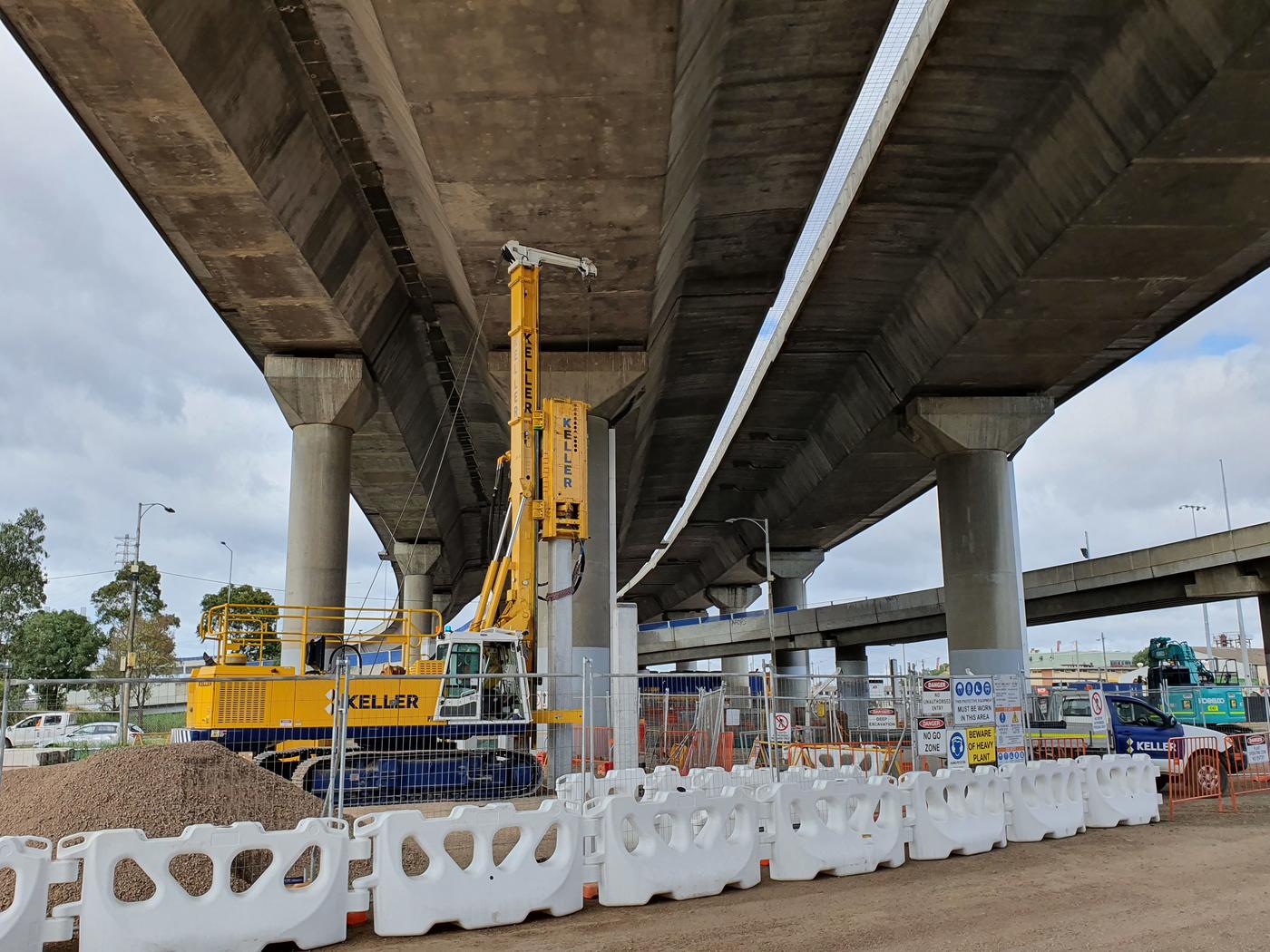
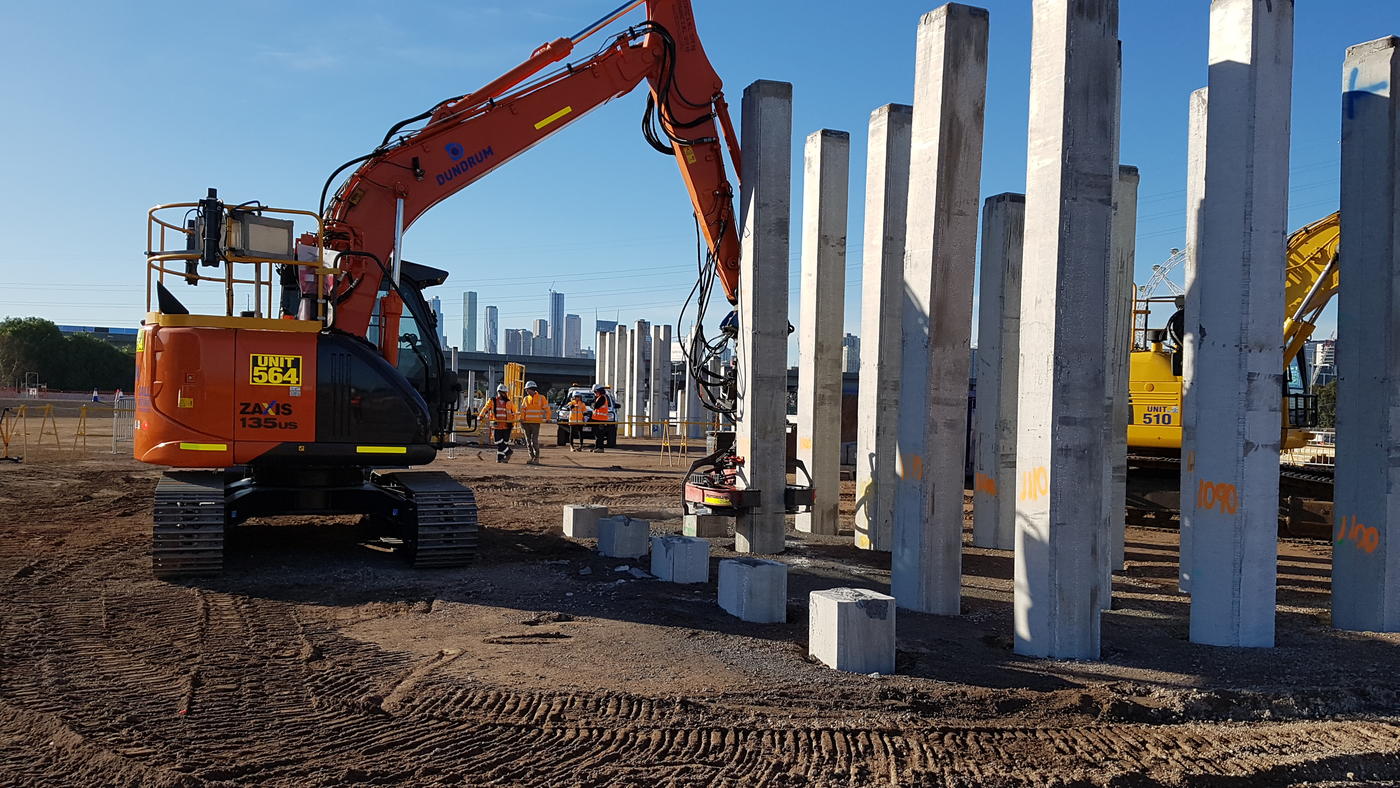